Exploring the Dynamics of Prototype Molding
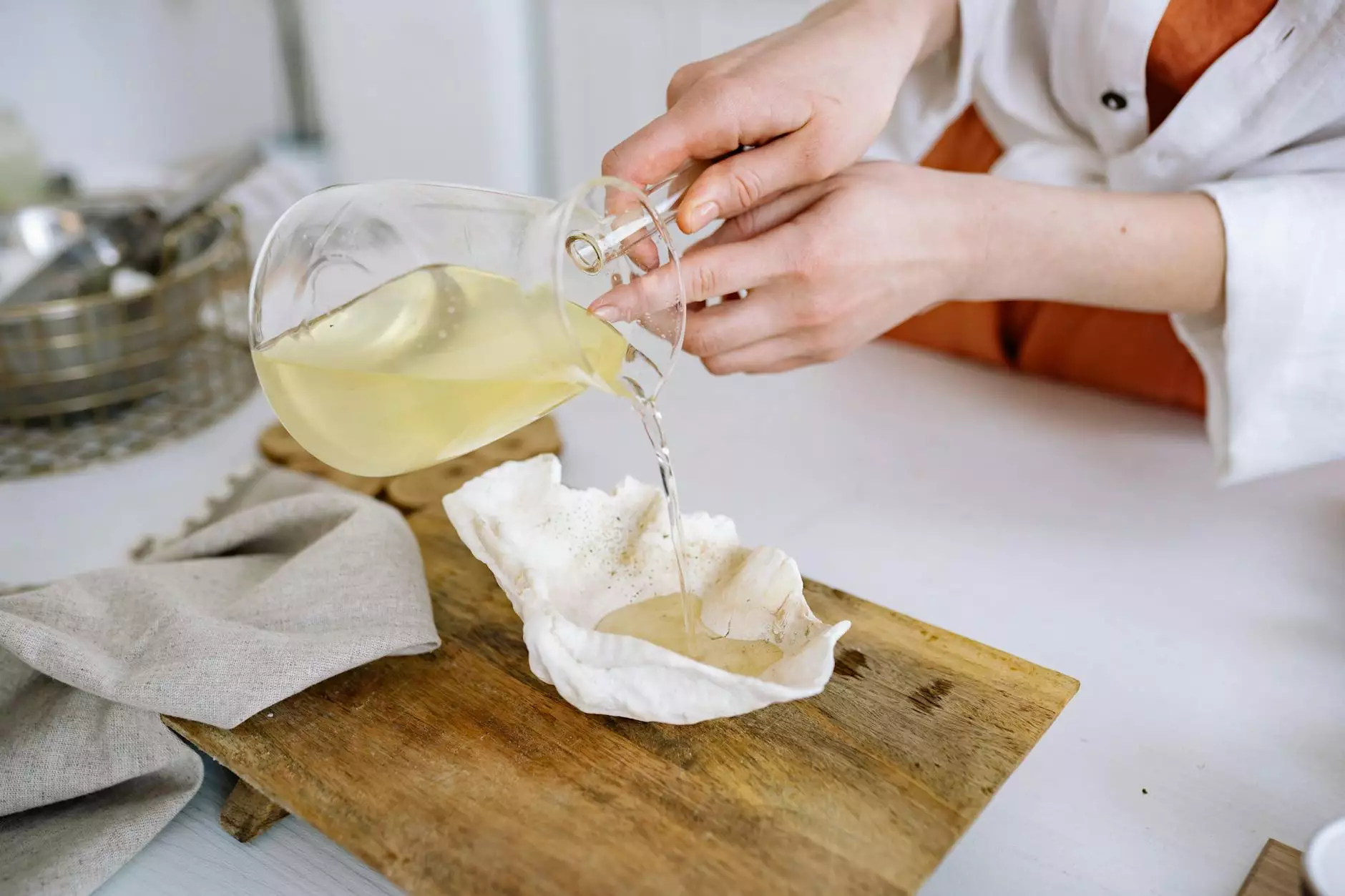
In the realm of manufacturing, especially in the sector of metal fabrication, the term prototype molding resonates with innovation, efficiency, and precision. The process of prototype molding is pivotal for designers and manufacturers who seek to transform their ideas into tangible products before commencing mass production. This article delves deep into the world of prototype molding, its processes, benefits, and its integral role in the metal fabrication industry, particularly as showcased by deepmould.net.
What is Prototype Molding?
At its core, prototype molding involves the creation of a prototype—a preliminary model of a product used for testing and validation of design concepts. This process typically employs various materials, including metals, resins, and plastics, tailored to meet specific project requirements. The significance of prototype molding can be seen in various industries, including automotive, aerospace, and consumer products, where precision and quality are paramount.
The Importance of Prototype Molding in Metal Fabrication
In the metal fabrication industry, prototype molding serves as an essential step in the product development cycle. It allows companies to:
- Test Designs: Manufacturers can evaluate the functionality and design of a product before committing to full-scale production.
- Identify Errors: Early prototypes help detect flaws in design and manufacturing processes, reducing costly errors down the line.
- Enhance Communication: Prototypes can bridge the gap between engineers and stakeholders, improving clarity and expectations.
- Accelerate Time to Market: By refining concepts through prototypes, companies can significantly shorten the product development timeline.
The Process of Prototype Molding
The process of prototype molding generally follows a set routine, encompassing several stages:
1. Concept Development
This initial phase involves brainstorming and sketching ideas based on the requirements and specifications provided by clients. It sets the groundwork for what is to come.
2. CAD Modeling
Once the concept is established, engineers create a Computer-Aided Design (CAD) model that serves as the blueprint for the prototype. This model allows for precise dimensions and details to be included.
3. Material Selection
Choosing the right material is crucial for prototype success. Whether it's aluminum, steel, or specialized alloys, the chosen material impacts durability, weight, and overall performance.
4. Prototyping Techniques
There are various prototyping techniques available:
- 3D Printing: Utilizes additive manufacturing to create prototypes layer by layer.
- CNC Machining: Involves subtractive manufacturing techniques to carve out prototypes from solid blocks of metal.
- Injection Molding: A method favored for producing plastic prototypes but can also be adapted for metal.
5. Testing and Validation
Once the prototype is ready, extensive testing is carried out to ensure its functionality and reliability. Feedback from testers can lead to further refinements.
6. Final Adjustments
Based on the feedback received, adjustments are made to enhance the design or functionality of the prototype, preparing it for potential mass production.
Advantages of Using Prototype Molding
Engaging in prototype molding offers numerous benefits that can significantly impact a company's success:
- Cost Efficiency: Creating prototypes reduces the risk of costly mistakes during the full-scale production phase.
- Improved Product Quality: Prototyping emphasizes quality control, leading to superior end products.
- Client Satisfaction: Providing clients with a tangible prototype boosts their confidence and satisfaction with the development process.
- Innovation: The iterative nature of prototype molding fosters innovation, allowing teams to explore new ideas freely.
Common Applications of Prototype Molding in Metal Fabrication
Prototype molding finds application in various sectors within metal fabrication. Here are some notable examples:
Automotive Industry
In the automotive industry, manufacturers use prototype molding to develop complex parts and components such as engine parts, body panels, and internal structures. This sector demands high precision and reliability, where prototypes allow for thorough testing before moving to production.
Aerospace Sector
For aerospace applications, the stakes are even higher. Prototype molding enables manufacturers to create lightweight yet durable components that meet stringent safety regulations. The ability to test prototypes in simulated environments is crucial for ensuring safety and performance in flight.
Consumer Electronics
The fast-paced world of consumer electronics thrives on innovation. Companies utilize prototype molding to develop new devices rapidly, ensuring they stay ahead of market trends and meet consumer demands.
Medical Devices
In the medical field, precision is critical. Prototypes are used for developing surgical instruments, implants, and diagnostic equipment, where the stakes involve human lives. Rigorous testing of prototypes ensures efficacy and safety.
Why Choose DeepMould for Prototype Molding?
DeepMould is a leader in the field of metal fabrication and specializes in prototype molding. Here are reasons to consider DeepMould as your go-to provider:
- Advanced Technology: DeepMould utilizes state-of-the-art technology in CAD modeling and prototyping techniques.
- Experienced Team: Their team comprises skilled professionals with years of experience in the industry.
- Quick Turnaround: They pride themselves on delivering high-quality prototypes in tight timelines, ensuring you stay ahead of your competitor.
- Comprehensive Support: DeepMould offers guidance from initial design to final production, ensuring complete client satisfaction.
Conclusion
In conclusion, prototype molding is an indispensable part of the metal fabrication industry, facilitating innovation and quality in product development. The ability to create and test prototypes can significantly save costs and time while enhancing product quality and client satisfaction. DeepMould stands out as a premier provider in this space, offering the technology and expertise necessary to bring your ideas to life through prototype molding. For detailed insights and further assistance, visit deepmould.net today!