Mastering Industrial Blower Design for Optimal Performance
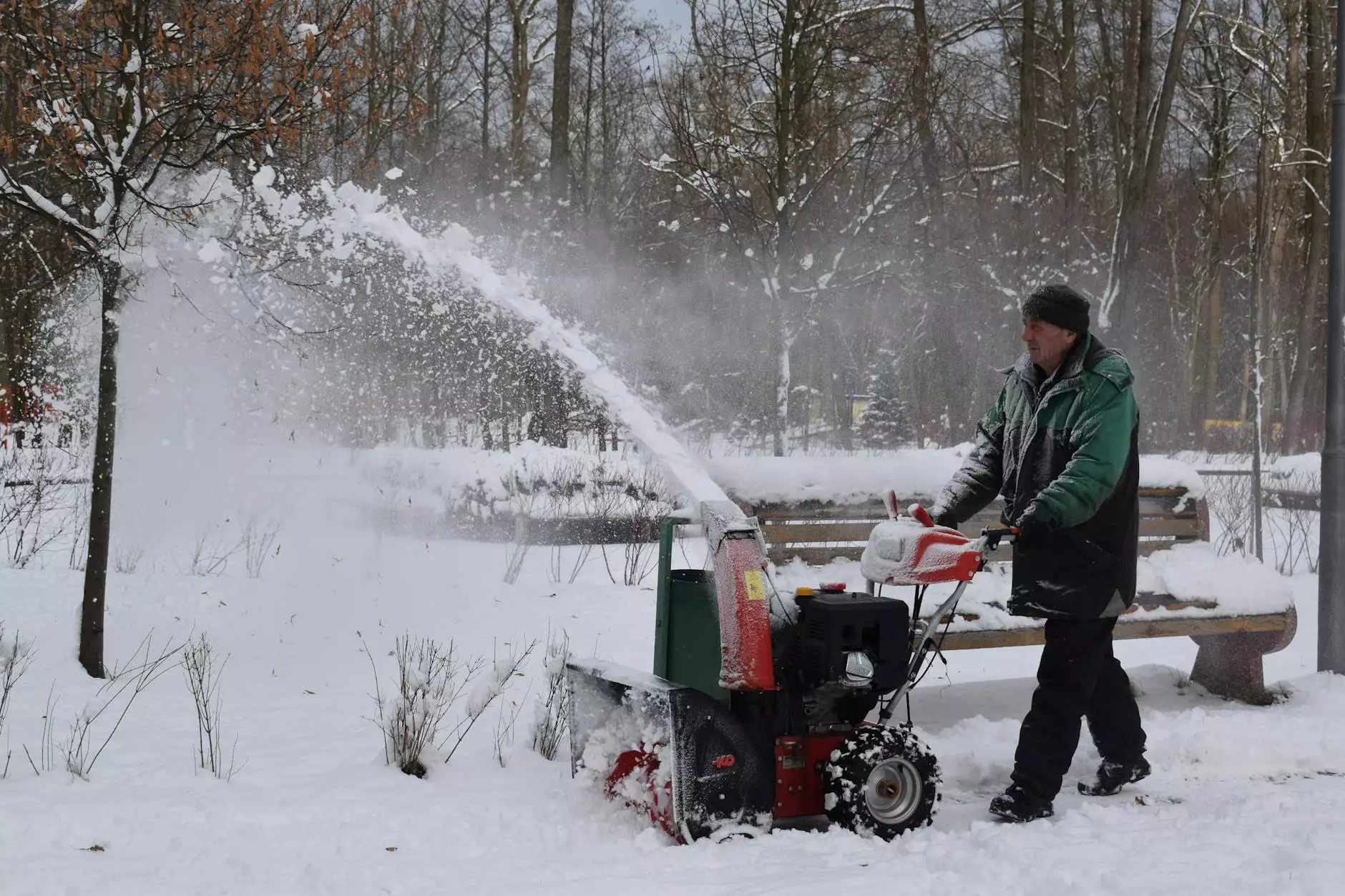
In the realm of industrial applications, blower systems play a pivotal role in ensuring efficiency and effectiveness across various processes. The concept of industrial blower design encompasses a diverse range of engineering principles, technologies, and applications that work together to optimize air movement for numerous purposes. This article delves into the significance, components, and advancements in industrial blower design while emphasizing how businesses, especially in the blow-dry services sector like TMM.com.tr, can enhance their operations through innovative blower solutions.
Understanding the Basics of Industrial Blower Design
Industrial blowers are mechanical devices used to move air and gases in various industrial settings. They are essential for processes such as ventilation, material handling, and drying, making the industrial blower design a crucial aspect of many manufacturing and service-oriented businesses.
The Components of Industrial Blower Systems
An effective industrial blower system consists of several key components, each contributing to the overall functionality and efficiency:
- Blower Housing: The outer casing that houses the internal components, protects them from external damage, and helps direct airflow.
- Impeller: A rotating component that generates airflow; its design directly influences the performance and efficiency of the blower.
- Motor: Powers the impeller to induce airflow; choosing the right motor is essential for optimal operation.
- Inlet and Outlet Ducts: Direct air into and out of the blower system, ensuring a consistent and efficient flow of air.
- Control Systems: Regulate the operation of the blower, enabling automation and enhanced efficiency in air movement.
The Importance of Proper Blower Design
Effective blower design is paramount for several reasons:
- Energy Efficiency: A well-designed blower system reduces energy consumption, leading to significant cost savings over time.
- Performance Optimization: Proper design ensures that the blower meets the specific airflow requirements of the application.
- Reduced Noise Levels: Advanced blower designs can minimize operational noise, creating a better working environment.
- Longevity and Reliability: High-quality materials and thoughtful design can increase the lifespan of the equipment, reducing the need for frequent repairs or replacements.
Applications of Industrial Blower Systems
Industrial blowers find applications in a multitude of sectors, including but not limited to:
1. Ventilation and Air Circulation
Blowers play a critical role in ventilating spaces, improving air quality in manufacturing plants, cafés, and commercial facilities. They are designed to move large volumes of air, ensuring proper circulation and comfort.
2. Drying Processes
In businesses that offer blow dry services, such as hair salons located at TMM.com.tr, industrial blowers assist in drying hair quickly and efficiently. These systems are engineered for high airflow and temperature control, providing clients with optimal service:
- Professional Blow-Dry Services: Utilizing high-performance blowers for streamlined operations.
- Hair Drying Efficiency: Reducing service time while maintaining hair quality.
3. Material Handling
In warehouses and factories, blowers are employed to convey dry bulk materials. Their design ensures the safe and efficient movement of these materials without compromising quality.
4. Environmental Control
Industrial blowers help maintain environmental conditions in manufacturing processes, controlling dust and particulate matter, thus promoting worker safety and compliance with regulations.
Factors Influencing Industrial Blower Design
The development of an industrial blower must consider several critical factors:
1. Airflow Requirements
Understanding the specific airflow needs is crucial. This includes determining the required volume and velocity of air to optimize performance for each application.
2. Pressure Requirements
Blower systems must be designed to generate specific pressure levels necessary for the intended application. This can vary significantly based on the operation being performed.
3. Operating Conditions
Environmental conditions, such as temperature and humidity, can impact performance, necessitating adaptive design approaches to address these variables.
4. Material Selection
The choice of materials influences durability, weight, and maintenance needs. Industries with corrosive environments may require specialized coatings or materials.
Design Innovations in Industrial Blowers
Advancements in technology have brought about significant innovations in industrial blower design. Some of these include:
1. Computer-Aided Design (CAD)
Utilizing CAD software allows engineers to create precise models of blower systems, facilitating efficient testing and modification before physical production.
2. Smart Controls and Automation
Modern blowers are equipped with smart controls that monitor airflow, temperature, and other parameters in real-time, enabling automated adjustments for enhanced efficiency.
3. Modular Designs
Modular blowers can be easily scaled or customized for various applications, providing flexibility in industrial settings that vary from project to project.
4. Use of Advanced Materials
Innovations in material science have led to the development of lightweight yet durable components, contributing to energy savings through reduced load on motors.
Choosing the Right Industrial Blower for Your Business
Selecting an appropriate industrial blower design involves consideration of numerous factors that align with business needs. Here are some tips for making an informed decision:
1. Assess Your Requirements
Determine the specific airflow and pressure needs of your application. Collaborate with engineers to figure out the best solutions suited for your operations.
2. Evaluate Efficiency Ratings
Look for blowers that demonstrate high efficiency ratings; this can impact long-term operational costs substantially.
3. Consider Maintenance Needs
Select designs that simplify maintenance processes. Systems recognized for reliability often require less frequent maintenance, saving time and resources.
4. Consult Industry Experts
Engaging with experts in industrial blower design will provide valuable insights tailored to your specific industrial or service-oriented needs.
Future Trends in Industrial Blower Design
The landscape of industrial blower design is continuously evolving. Some promising future trends include:
1. Sustainable Manufacturing
As industries become increasingly eco-conscious, the demand for blowers that meet sustainability standards is rising, prompting innovations that enhance energy efficiency and reduce waste.
2. Integration of IoT Technologies
The Internet of Things (IoT) is beginning to play a significant role in blower systems, allowing for enhanced monitoring and predictive maintenance capabilities.
3. Customized Solutions
As every industrial operation is unique, the future will likely see an increase in tailored blower design solutions that cater specifically to the individual needs of businesses.
Conclusion
In conclusion, understanding the nuances of industrial blower design is vital for optimizing performance across various applications. For businesses focused on providing blow dry services, such as those operating under the banner of TMM.com.tr, investing in innovative and efficient blower designs can significantly improve service delivery and customer satisfaction.
As the industry evolves, staying abreast of new technologies and practices will be essential for sustaining a competitive edge. Embrace the advancements in blower design to maximize your operational efficiency, reduce costs, and enhance the quality of your services.